Brought to you by Stefan Sädbom from Lovisagruvan
Experiences from the “the real, the hard, mining waste rock world”.
Lovisagruvan AB is one of the 28 partners in the FutuRam consortium and is an operating zinc-lead and silver producing mine in South Central Sweden. Lovisagruvan also has interests in the nearby Håkansboda historical mining area where copper, cobalt, gold and silver have been extracted between 1328 and 1912.

Potential
Amongst the widespread piles of waste rock, it is easy to find specimens that contain minerals that in turn contain copper, cobalt, silver, zinc, iron, and other more exotic elements like bismuth, antimony, molybdenum, and even some gold, as well as deleterious elements like arsenic. It is easy to imagine that some of these specimens “must be” worth extraction, but is it realistic?
“Realistic” in this case means that not only technical-, environmental-, ecological-, heritage- and economical-requirements must be met, but it must also be legally permissible. Can all this be accomplished and is the combined effort balanced by the value of the extracted secondary raw materials? At the moment, the answer is: “we don’t know!” Lovisagruvan is trying to get to the bottom of this question in close cooperation with SGU (Swedish Geological Survey) and GTK (Geological Survey of Finland) by studying the important aspects hoping to get closer to the combined answer.
So far, efforts have been made to map the occurrence, distribution, grades, tonnages, variation, mineralogy, grain size etc., which is important information that must be “on the table” to enable a meaningful study to be developed.
Technical Feasibility
Once estimated, different technical aspects must be examined: Which minerals are “carriers” of valuable elements? How are they distributed and how can they be identified and recovered? At what cost and environmental impact can they be recovered? What is the margin once all cost has been deducted?
It is too early to answer most of these questions, but one can already ponder if there are other, “non-monetary” values that should be added to the (positive or negative) side of the equation such as: What is the value of current negative environmental impacts that may be removed with the extraction of valuable secondary raw materials? What is the value of a secondary recovered raw material versus imported primary raw materials? These questions must be addressed and assessed before we are even close to doing the calculation.
On the technical side, we now have a decent idea of the gross distribution and content of the rock mining waste piles at Håkansboda and made a first trial test to evaluate the gross extractability by some of the more common methods used for extraction of sulphide minerals (which in this case are the main carriers of valuable elements).
Preliminary Conclusions
One preliminary conclusion is that standard methods don’t work particularly well, and that is probably due to these methods being tailored for primary, freshly extracted material. Material that has not been exposed to weathering and oxidisation for hundreds of years. Of course, scientists have an array of methods to overcome the problem at lab-scale, but will it work in full scale?
One challenge is that historical miners overall have been quite effective. Although it is possible to find nice looking hand specimens rich in metals, and “hot spots” where grades are above the average, the overall grade remains relatively low.
Is it possible to upgrade the material on site before it is sent to an (often far off) “enrichment plant”?
Current Process
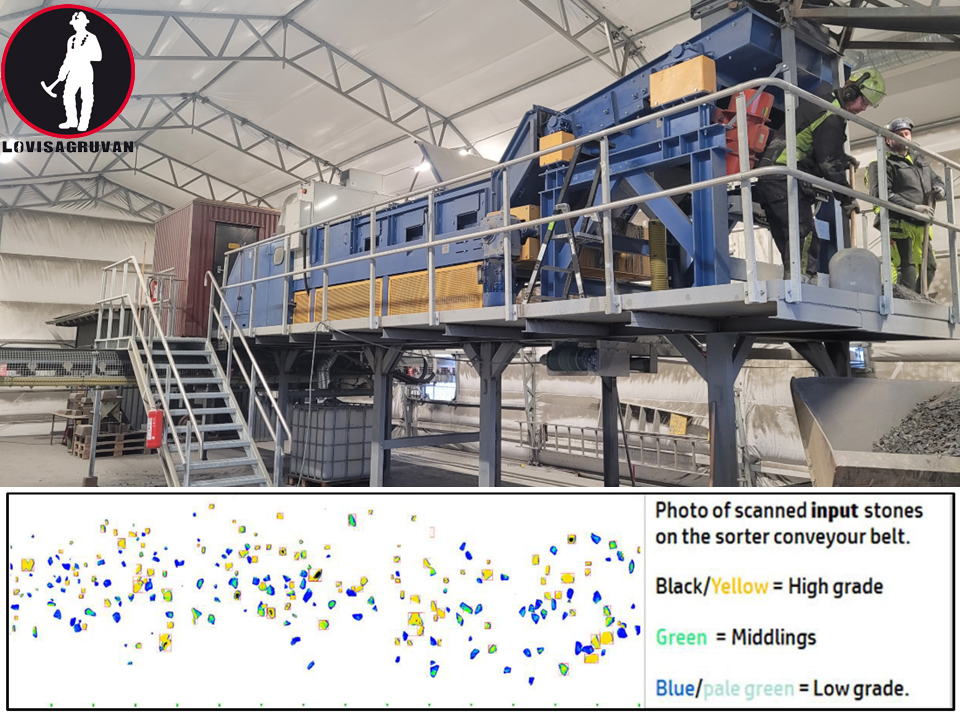
At Lovisagruvan, the primary ore is upgraded in a “sorting plant” where penetrative x-rays are used to separate pieces of rocks that contain “ore material” from waste rock. This method is tailored for the minerals of Lovisagruvan (different to those at Håkansboda). However, since this method, simply put, can be based on an equivalent to density, it might very well have good potential in aiding the upgrading of historical mining rock waste as well.
Test Results
Between 2023 (winter) and 2024 (spring) several hundreds of kilos of mining rock waste of random composition were collected and, after pre-treatment (crushing and sieving of fractions etc.), the performance in the sorting plant was tested using standard Lovisagruvan settings.
Out of a total of 700 kg, some 420 kg was amenable to sorting after crushing and size-screening. The feed material had a copper grade (copper grade is in this case used as a proxy for “valuable minerals”) of 0.46% Cu. After sorting, 60% of the mass had been separated as a product now containing a copper grade of estimated 0.6% Cu (which is a ~30% increase). An estimated 18% of the total copper content was “lost” to secondary waste, but since this trial was done using standard settings for different type of minerals, the results were interpreted as being rather promising!
The trial is still being evaluated, but a preliminary conclusion is that different methods of sorting on/near site, may be an important part of the processing chain and sorting may have the potential to significantly reduce transportations cost (40% less mass to transport) from the historical mining waste site to a processing plant.
The test has only examined a small part of the theoretical value chain between a deposit of secondary raw materials in mining waste to the full recovery of valuable components but has given a valuable piece of information that may help solve the big puzzle!